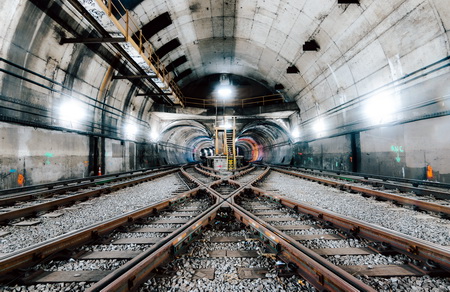
Did you ever wonder how a tunnel is created? Well, you’ve come to the right place.
Human ingenuity has taken us from the industrial revolution to space exploration, but it has also taken us underground, from the giant Bagger 293 bucket wheel excavator for mining to machines that crush through the dirt to make tunnels deep below the surface.
A Little Tunnel History
In the earlier days, boring through the underground required many hours of tedious labor. It was not just the dig that was time-consuming but buttressing the area around the tunnel so that it stayed safe was also tedious.
Men would create concrete rings and secure them along the top of the tunnel and alongside the walls. This would ensure that the tunnel didn’t weaken and collapse.
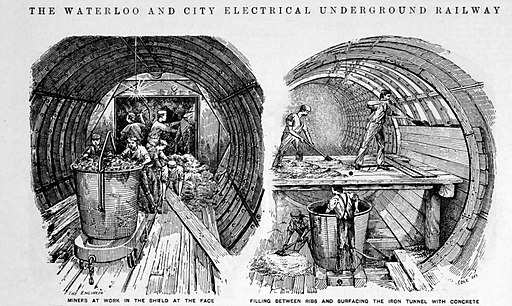
The process of securing the tunnel by hand was the normal way of doing things back in the day, but now, all that hard, unhealthy labor is a thing of the past. Why? Enter the tunnel boring machine (TBM).
The Tunnel Boring Machine

If there was ever a device that one would call a machine, the TBM would be just that. Large, noisy but effective, it is used to cut through soil and rock much like a power saw is used on wood. As the saw’s steel blade spins, it cuts right through the wood, which is similar to the job of the boring machine, only larger. Much larger!
How Does the TBM Work?
The machine consists of three major parts (actually, a lot more, but we’ll keep it simple so that we don’t bore (pun intended) you with all the intricate details).
The Three Parts are:
- Cutter-head (front)
- Tunnel shield (middle)
- Trailing gear (rear)
Of course, each of these sections is made up of smaller parts and together they comprise the boring machine.
The Cutting Head
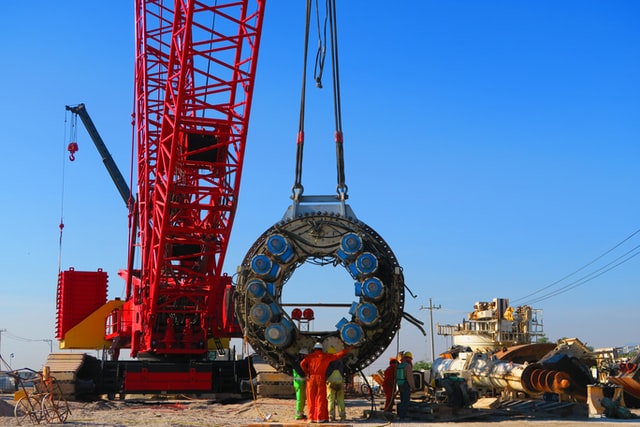
We spoke about the saw, but what does this saw have that cuts the wood so precisely? It is a circular piece of steel with cutting blades.
For the TBM, they are called disc cutters and are integrated onto the edges of a round piece of steel. For the TBM, the cutting head is located at the very front of the machine.
As the boring machine’s cutter-head rotates, it breaks through the rock and/or soil at a rate of 2.7 revolutions per minute and at a pace of about 50 feet per day.
The machine looks like a giant worm, expanding about 272 feet in length. It is this long because after the soil is extracted, it is sent down long conveyor belts where it is extracted to the surface and carted away. See these videos below, which provide expert explanations about how the Tunnel Boring Machine operates.
The Tunnel Shield
A tunneling shield is a cylindrical protective structure that is located just behind the cutting head and is used to shelter the workers from the dangers of falling dirt and debris and/or actual collapse of the tunnel.
The shield is used as a temporary support structure until the tunnel is secured with concrete (see Tunnel Rings below). The first shield was designed by Marc Isambard Brunel and was rectangular in design with iron scaffolding and consisting of three levels. Then it was later modified into a cylindrical form, which is what is used today.
What are Tunnel Rings?
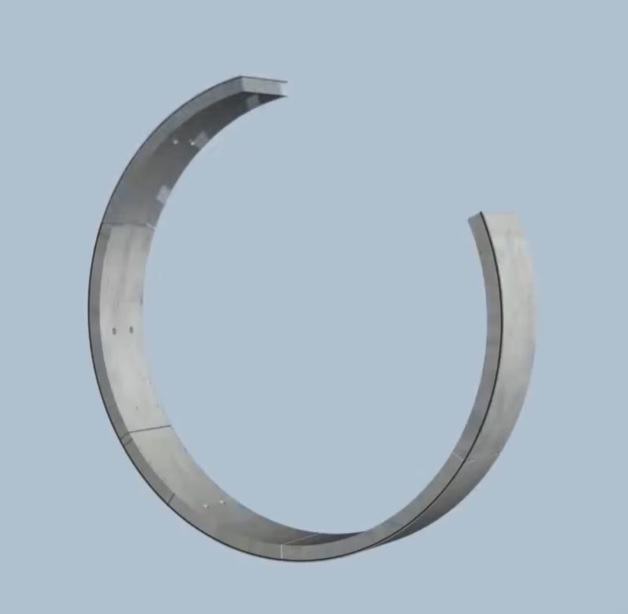
The tunneling shield is designed to be used only until the tunnel is safely secured with a more permanent process; as such, prefabricated concrete rings are secured along the roof and sides of the tunnel to stabilize it and turn it into a permanent structure. The process begins when the cutting head stops spinning, synchronized to do so each time a new set of rings are needed to be installed.
A robot called an erector lifts each ring and sets it in place along the tunnel lining, resulting in a solid cylindrical wall of concrete at the top and along the sidewalls, subsequently maintaining the structural integrity of the tunnel.
The rings are assembled as segments from above-ground factories. They are transported from the factory to the tunnel location, moved down into the tunnel and onto the boring machine where the erector lifts them and secures them inside the tunnel.
Precast molded lining sections were first patented in 1874 by James Henry Greathead, a mechanical and civil engineer famous for his work on the London Underground. Greathead also improved the tunnel shield from its rectangle form into its current form of cylindrical steel.
This process of cutting through the dirt then stopping so that the rings can be installed alternates every 5–7 feet. The cutting heads spin, evacuating the earth in front of it, then stops and the erector builds the supporting rings and then the cutting head begins to spin again, moving forward at its slow but efficient pace.
Trailing Gear
How Does the Evacuated Dirt and Rock Get Taken Out from Underground?
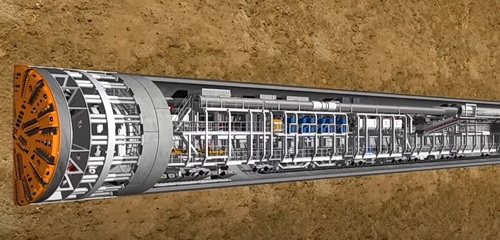
Enter the trailing mechanisms. They include a conveyor belt that removes the soil that was excavated from the cutter head. As the cutter pulls dirt out, it places it onto a belt conveyor which consists of a machine belt, cross belt and a tunnel belt. The tunnel belt is dynamic, in that it expands as the machine digs forward. The tunnel belt can expand up to 18 miles back to the extraction point where the soil is lifted to the ground.
The first two belts, the machine and cross belt are located at the very front of the TBM and the tunnel belt is the conveyor that moves the debris through the TBM to the area where it is taken out of the tunnel.
Summary
The engineering that goes into the assembly of a tunnel boring machine is quite sophisticated, but fascinating as well.
In this article, we simplified the process so that it can be easily understandable and we hope you were able to gain a good understanding of how tunnels are created, so the next time you drive through a tunnel or ride through the subway, you can be grateful for the ingenuity and hard work of the people who built it.