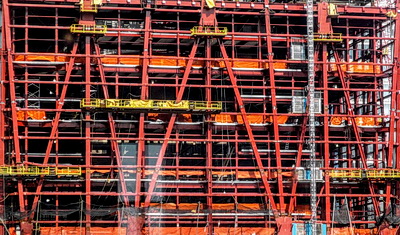
Walk down any city construction site, and you’ll see a network of steel beams and columns rising from the ground. Why are they using steel? Because steel is strong, durable, and easy to work with. It is the iron alloy of choice for building construction.
If you’re wondering how steel is manufactured, look no further! This blog post will explain the process from start to finish.
History of Steel
The emergence of steel can be traced back to the Iron Age when it was used to make swords. History experts say that the original creators of steel were the Hittites. This Middle Eastern civilization existed during the Bronze Age and later into the Iron Age, between 1400 and 1200 B.C., in Syria and Turkey. They learned that heating iron with carbon could make a stronger metallic substance.
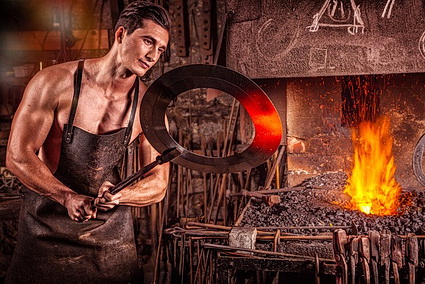
Historians are not exactly sure what happened to the Hittites, but the consensus is that they most likely morphed into the Neo-Assyrian Empire (912 to 612 BC).
It has also been discovered that China first worked with steel around 403–221 BC. The Han dynasty (202 BBC—AD220) melted wrought iron with cast iron, producing a steel composite.
Modern Day Uses
With the advent of the railroad construction boom in the 19th century and its ongoing requirement for metal to make the tracks, a supply issue materialized. The process was slow and tedious since there wasn’t an automatic process to fill the need.
Enter the Steel Mill
Steel mills provided the raw materials for many of the world’s most essential products. Since the first mill opened in the early 1800s, they were constantly improved and adapted to meet the needs of the times.
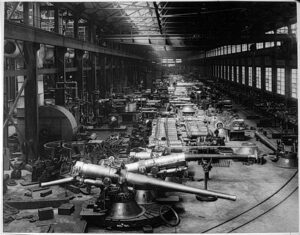
These manufacturing plants have helped build skyscrapers, bridges, and countless other structures. They have also been instrumental in developing new technologies, solving railway construction issues, and building assembly lines for other products.
No time was more profitable for the steel mill than during the Industrial Revolution, which began in the nineteenth century and continued until the mid-twentieth century.
And there wasn’t a company more notable for achieving the country’s manufacturing demand than Bethlehem Steel, which provided the product for 125 years, starting in 1887.
Enter the Skyscraper
Before steel was invented, the average office or apartment building would not reach more than five stories. Still, steel provided enormous strength and durability and, as such, allowed the construction of buildings taller and stronger than ever before.
How Steel is Made
Steel does not grow out of thin air. It begins with mining iron ore, which is then combined with carbon via a blast furnace. Let’s get more involved in understanding how this process works.
Mining the Iron Mineral
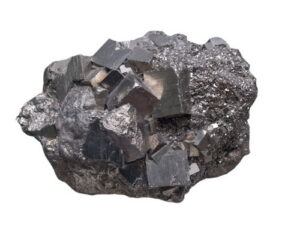
An ore is a natural substance found in the Earth’s service where the iron mineral can be extracted. Once the ore is removed from the quarry, it is melted and purified in a blast furnace (removing impurities and leaving only the metal).
Enter Carbon
Carbon is an element in the Periodic Table with an atomic number of 6, with four electrons in its outer shell and two in its inner shell.
Atoms with less than eight electrons in their outer shell (called the valence shell) tend to look for other atoms to bond with so that their outer shells can stabilize the atom by balancing the shell to eight electrons. This is based on the Octet Rule.
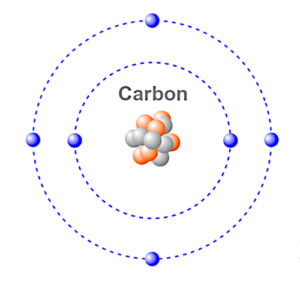
Iron has eight electrons in its valence shell, so if you bond the carbon atom, which has six valence electrons, with the iron atom, you have a molecule of two different atoms, which forms steel.
It is essential to ensure that the correct amount of carbon, approximately 0.04%, is used with iron so that the resultant product is steel.
If the wrong amount of carbon is mixed with iron, a different product will be produced, such as cast iron or wrought iron—both are inefficient in rendering steel.
Combining the Carbon with Iron Creates a Stronger Material
For steel, the two elements are combined while the iron metal is liquid hot, which alters the iron’s properties to that of steel. As a result, steel becomes an alloy (a metal made by combining two or more metallic elements) of iron and carbon.
This causes a distortion of iron’s crystalline lattice structure and subsequently enhances the metal’s strength; specifically, it increases the metal’s tension and compression properties.
The Manufacturing Process
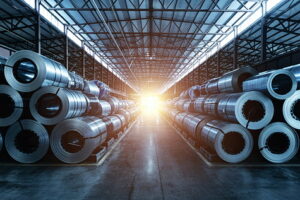
A breakthrough for manufacturing steel via an automated process materialized in 1856 when Henry Bessemer found a way to manufacture steel quickly. Bessemer’s steel production process is what inspired the Industrial Revolution.
It was the first cost-efficient industrial process for the large-scale production of steel from molten pig iron, using an air blast to remove impurities.
Adding Carbon Produces a Variety of Iron Alloys
As previously mentioned, iron’s characteristics change when mixed with carbon, allowing various types of metal alloys to be created. The amount of carbon added to iron changes its characteristics accordingly.
Cast Iron
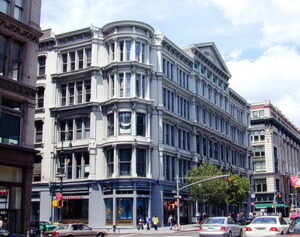
Cast iron is an alloy of iron that contains 2 to 4 percent carbon, along with smaller amounts of other elements, such as silicon, manganese, and minor traces of sulfur and phosphorus. These minerals are nonmetallic and are referred to in the industry as slag. Cast iron can be easily molded into a desired shape, known as casting, and has been used to make decorative fences and other aesthetic forms.
Cast iron facades were invented in America in the mid-1800s and were produced quickly, requiring much less time and resources than stone or brick. They were also very efficient for decorative purposes, as the same molds were used for many buildings, and a broken piece could be quickly remolded. Because iron is powerful, large windows were utilized, allowing a lot of light into buildings and high ceilings that required only columns for support.
Wrought Iron
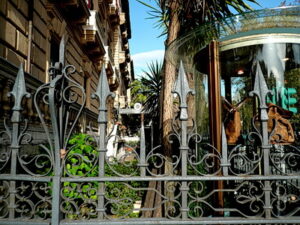
Photo: © SMS
Wrought iron is softer than cast iron and contains less than 0.1 percent carbon and 1 or 2 percent slag.
It was an advancement over bronze and began to replace bronze in Asia Minor by the 2nd century BC. Because iron was far more plentiful as a natural resource, wrought iron was used for various implements, weapons, and armor.
Steel
Steel is an alloy made from iron that usually contains several tenths of a percent of carbon, which increases its strength and durability over the other forms of iron, especially in tensile strength.
Strictly speaking, steel is just another iron alloy, but it has a much lower carbon content than cast iron and about as much carbon (or sometimes slightly more) than working iron, with other metals frequently added to give it additional properties.
Most of the steel produced today is called carbon steel, or simple carbon, although it can contain metals other than iron and carbon, like silicon and manganese.
Stainless Steel
The steel alloys mentioned above have carbon integrated within them, but stainless steel uses chromium as its alloying element. The result is that each produces a very different result when it comes to corrosion resistance. Stainless steel is much more corrosion-resistant.
Galvanized Steel
Besides incorporating the general benefits of steel, galvanized steel has an added corrosion resistance strength by integrating a zinc-iron coating. The zinc protects the metal by providing a barrier to corrosive environmental elements.
Summary
The advantages of steel are numerous, from great tensile and compression strength to the speed of manufacturing to low cost; it is the metal of choice in construction when compared to iron.
Although iron and steel appear similar, they are two distinct materials with specific characteristics and qualities. Iron is a pure mineral, and steel is an alloy material that contains a percentage of carbon. Different products emerge depending on the amount of carbon mixed with iron, including steel creation.
Steel is a far stronger material, and there is no better metal currently used when strength and cost are major factors.